Workplace accidents involving concrete pumping equipment can result in significant injuries, permanent disability, or even death. Concrete pumping accidents can result from:
- Mechanical issues
- Environmental hazards
- Operator carelessness
This guide will provide you with the essential information you and your operators need to identify potential hazards, take the necessary steps to mitigate them, and prevent accidents before they occur.
Inside this guide:
- Types of concrete pump safety hazards
- Concrete pumping safety precautions
- Concrete pump safety tips for operators
- The unsung hero of concrete pump safety
- Key takeaways
Types of Concrete Pump Safety Hazards
Awareness of the most common concrete pumping hazards is the first step toward working safely. Here are seven of the most common concrete pumping hazards, and some pro tips for overcoming them on the job.
Hose Hazards
Hoses are a central component of concrete pumping systems, so they're also responsible for a large chunk of concrete pumping accidents. Even when not in use, concrete delivery hoses can still contain large amounts of concrete. The largest concrete delivery hoses can weigh up to 376 pounds when filled.
Concrete hose-whipping events occur when compressed air inside the hose causes it to come untethered and whip around violently. If a hose is not correctly constrained, it can go from vertical to horizontal in around 0.3 seconds! This momentum, combined with the heavy weight of its concrete and metal ends, will result in significant injury or even death for anyone it hits.
Pro Tip: Avoid hose-whipping accidents by maintaining a safe physical distance from a hose when air is in the system and make sure the hose doesn’t get too close to anything else in the area.
Power Lines
Power lines in your working environment can present a major hazard. If your concrete pumping machinery comes into contact with a live power line when in use, it can cause severe burns, injuries, or even death for its operators.
Pro Tip: Avoid accidental power-line contact by identifying the locations of any power lines in a work environment beforehand. Power-line stamps are a useful tool on job sheets or in information logs. This helps all of your operators recognize the presence of power lines and avoid them during pumping operations.
Electrical Hazards
In addition to power lines, concrete pump trucks themselves are a common cause of electrical issues on the job site.
Pro Tip: Prevent electrical accidents by performing routine maintenance on each truck’s batteries and electrical system to identify and prevent electrical problems before they occur.
Concrete Burns
While most concrete pump operators are familiar with the dangers of flying debris and moving equipment, not enough realize that they may also be at risk of chemical burns. But liquid concrete can and does cause injury to many concrete operators who don’t follow adequate safety checklists.
Exposure to liquid concrete is a major hazard for all concrete pump operators. When liquid concrete comes in contact with your bare skin, it can cause injuries that range in severity from irritating rashes to major third-degree burns.
Pro Tip: Avoid concrete burns by always wearing appropriate safety gear when operating pumping equipment. Personal protective equipment such as eye protection, gloves, and long-sleeve shirts can also help keep operators safe from concrete burns.
Hydraulic Leaks
A hydraulic leak in your concrete pumping equipment can be a significant risk to all of your operators. When your equipment’s hydraulic system springs a leak, the oil inside can burst out at extremely high speeds, which can damage equipment or the skin of anyone nearby. Operators who suffer a hydraulic leak accident can experience severe burns or even death.
If you experience a hydraulic leak, the first thing to do is stop the leak as soon as possible. Catch as much of the leaking oil as possible, taking care to switch to a new bucket before each bucket fills to the brim. However, the best way to deal with hydraulic leaks is to prevent them from happening in the first place by regularly checking hydraulic equipment for any small damage that could turn into a major leak.
Boom Accidents
Many concrete pumps use boom lifts to carry operators up to the equipment controls or machinery located in high places. But while these lifts are often an essential aspect of the job, they still pose a significant safety hazard to operators who don't follow safety precautions.
Most accidents involving boom lifts occur when operators need to pay more attention to their surrounding area. A boom colliding with another object or structure during the concrete pumping operation can cause major damage or injure anyone nearby.
Pro Tip: Boom lift operators should always look out for potential hazards or obstructions before operating their lifts. Common hazards include power lines, lights, sprinklers, and HVAC systems. Overall, the best way to prevent boom lift accidents is to be “boom aware” at all times, before and during boom lift operations.
Rough Mixes
As concrete mixtures become more complicated, the risk of rough mix accidents becomes more and more likely. These accidents occur when your concrete mix does not have the correct components or proportions for your specific equipment or pumping needs. Not only can these cause damage to your equipment, but rough mixes can also potentially injure your operators during the pumping and maintenance processes.
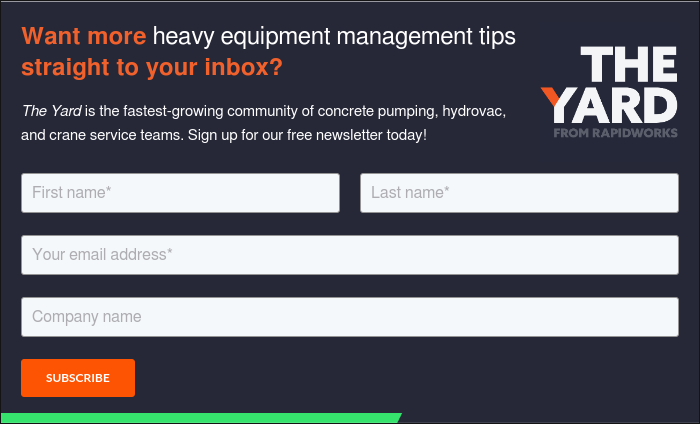
Concrete Pumping Safety Precautions
Once you and your operators have a good understanding of the main hazards they may face on the job, the next step is to identify the best concrete pump safety precautions you can take to reduce the risk of accidents.
In any area of heavy machinery operation, the safest teams are always the best-prepared teams. The following concrete pumping safety precautions will help your operating team stay aware of potential hazards and prevent accidents before they occur.
Outrigger Pins
Outrigger pins are a small but vital component of concrete pumping equipment. Because they're easy to overlook, operators too often neglect potential issues with their outrigger pins. But outrigger pin failures can result in major accidents and injuries to your operators. Concrete pump operators can avoid these accidents by always checking to make sure that the outrigger pins are pinned and locked before traveling.
It’s also a good idea to perform routine checks of your equipment’s outrigger pins to make sure all of them are in good condition. If you can identify damaged or worn pins, you can replace them before they cause any accidents.
Water Box Safety
Your pumps’ water box covers can present crushing and amputation hazards to your operators. These accidents often occur when operators remove water box covers or grates while the machine is in operation. Your operators can avoid water box cover accidents by always stopping pumping before removing water box covers to add or replace water.
Hoisting
Operators sometimes forget or ignore the fact that concrete pump booms are not authorized for use as a crane or hoisting device. If operators use booms for anything other than their intended purpose, this can cause dangerous collapses, falls, or potentially fatal accidents. Insurance companies may also refuse to provide compensation for accidents caused by the misuse of equipment.
Your operators can easily avoid these kinds of accidents by taking note of the specific purpose and designated usage of booms and other kinds of equipment. Safe usage of concrete pumping equipment is always the correct use of concrete pumping equipment.
Safety Slings
All items suspended from a boom should be attached to an appropriate safety sling. Sometimes, if one of these slings breaks or ruptures during a job, the operators don’t want to bother with the hassle of stopping their pumping to replace it. Unfortunately, this attempt at a shortcut is an all-to-common cause of accidents. Operators can avoid such accidents by paying close attention to all safety slings and immediately stopping their pumping operations if one breaks.
Underwater Pumping
Underwater concrete pumping can present a unique set of safety hazards for your operators. You can avoid these hazards by following specific safety precautions when pumping concrete in water. Check that all placing lines are primed, or “grouted,” to ensure no water comes into contact with the priming material.
You should also avoid letting the discharge end of the placing system rise above the level of the concrete itself. If operators don’t follow this protocol, water can get into the concrete and reduce its structural soundness.
Cold Weather Pumping
Any cold-weather operations can present specific environmental hazards that your operators should know about. Working in extremely cold conditions can cause hypothermia or frostbite without proper cold-weather precautions. Your operators can avoid cold-related injuries by wearing several layers of cold-weather clothing.
Concrete Pump Safety Tips for Operators
A basic understanding of the major safety hazards and precautions is vital, but concrete pump operators can go one step further by keeping a detailed safety checklist for each job site. Even for operators who understand the main hazards they may face, it’s easy to let important safety protocols slip on the job.
A good concrete pump operator safety checklist should include protocols for all of the major safety hazards inherent to that job. The following list is a great starting point for building your own safety checklist, though you can always include additional safety protocols as needed:
- Heat safety: If your operators are working in hot conditions, make sure they have cool, loose-fitting clothing and plenty of fluids on-site to stay hydrated. This can go a long way in preventing heat-related injuries like heat exhaustion or heat stroke.
- Cold safety: For cold work environments, you can prevent hypothermia, frostbite, and other cold-related health hazards by making sure that your operators are wearing gloves, coats, and other types of appropriate cold-weather gear.
- Mounting/dismounting: Many concrete pumping accidents occur during mounting and dismounting. Before pumping, check to ensure that no one attempts to mount the equipment while it's in motion. You should also make sure that your operators always follow the “three-contact rule” (one hand on the equipment and two feet on the ground, or two feet and one hand on the equipment, at all times).
- Hearing protection: Hearing damage is an often-overlooked hazard for concrete pump operators. Pumping equipment is often loud, and prolonged exposure can cause permanent hearing damage. By including it on your safety checklist, you can make sure that your operators always have adequate hearing protection gear before they put their ears at risk.
- Eye protection: Operators can avoid eye injuries by checking to make sure that everyone on-site has adequate eye protection. Good eye protection gear will keep everyone’s eyes safe from flying dust, debris, and chemicals during pumping.
- Personal protective equipment: It’s often too easy to overlook inadequate personal protective equipment. If this happens, you may not realize that one of your operators is missing the necessary equipment until an accident occurs. Fortunately, making sure that everyone has appropriate protective gear is even easier if you include a thorough equipment inspection on your safety checklist.
- Standing between mixers and pumps: Operators should never stand between mixers and pumps during the pumping process, where drivers won’t be able to see them. Double-check that no one else is in the wrong position, and always maintain eye contact with drivers during positioning.
For more detailed concrete pumping safety tips for your crew, check out our concrete pump operator safety checklist.
Maintenance: The Unsung Hero of Concrete Pump Safety
You can easily avoid many common concrete pumping accidents through routine maintenance on your equipment. Although performing regular maintenance checks may seem expensive and time-consuming, in the long run it’s much better than suffering the fallout of a major accident resulting from improperly maintained equipment.
Here are a few heavy equipment maintenance tips that will keep your equipment in good working order and help you avoid workplace accidents:
- Keep your concrete pumps clean at all times. When inspecting a clean pump, you can more easily see and identify cracks and hydraulic problems.
- Regularly replace hydraulic and pipeline components.
- If you change the pressure during testing, make sure you always return it to the manufacturer’s specifications.
- Reinstall all safety pins to the delivery line clamps.
- Consult the manufacturer’s recommendations before changing or modifying the hydraulic pressure settings.
- Thoroughly document all maintenance.
Overall, concrete pump operators should follow all of the essential maintenance protocols that come with any heavy equipment. You can check out our Ultimate Guide to Heavy Equipment Maintenance for more tips on building a maintenance program that keeps your trucks on the road.
Key Takeaways
Ensuring safe working conditions is a shared priority for owners and operators on the job site, and it’s a shared responsibility, too. Getting familiar with the potential hazards of the work environment empowers all operators to make informed decisions about the right precautions to take. Make sure your team is educated and aligned on maintenance, protective equipment, and procedures so everyone can work together to get the job done safely.
RapidWorks' concrete pumping software helps operators complete all of their safety checks right from their phones so there’s never a reason to skip an inspection or safety assessment. RapidWorks' software also provides management with comprehensive records of all safety checks for future safety audits. If you’re serious about safety, check out RapidWorks today!
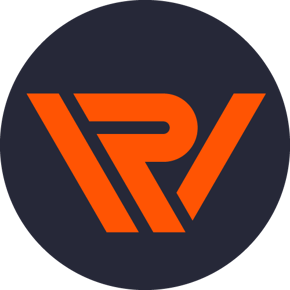