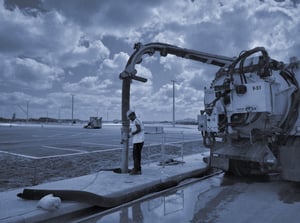
The Essential Heavy Equipment Maintenance Checklist
For heavy equipment teams, keeping your equipment in top shape is a constant battle against the elements. The daily grind of pressure, dust, heat, and constant use wears down parts faster than you can say "construction." That's why understanding the ins and outs of heavy equipment maintenance is crucial — it can be the difference between preventing a breakdown before it happens, and an unexpected repair that breaks the bank.
In this post we'll share our essential checklist for heavy equipment maintenance, from standard engine upkeep to technical maintenance for specialty equipment like concrete pumping and hydrovac trucks. We'll also show why heavy equipment maintenance is so important and how it can benefit your company, then give you some tips on how to create a heavy equipment maintenance strategy. Read on to learn more!
Inside this article:
- What Is Heavy Equipment Maintenance?
- Why Preventative Heavy Equipment Maintenance Matters
- Heavy Equipment Maintenance Inspection Checklist
- Specialty Equipment Maintenance
- 4 Easy Steps for Heavy Equipment Maintenance
- Tracking Preventative Maintenance
- FAQs
What Is Heavy Equipment Maintenance?
Heavy equipment job sites are harsh environments — things like dust, heat, extreme pressure, and constant use can cause parts to wear down extremely quickly. Heavy equipment maintenance includes anything you do to keep your trucks performing properly on the road and on the job site (one of the most important parts of maxing out your fleet utilization).
There are two main types of heavy equipment maintenance:
- Corrective maintenance, which usually involves tasks such as repairs and part replacements -- anything that gets equipment back up and running after a breakdown.
- Preventative maintenance, which usually involves regularly inspecting and caring for equipment before it breaks down. It can help you avoid repairs and downtime, and even extend the life of your equipment.
Corrective maintenance is usually geared toward things like repairs and part replacements that get equipment back up and running after a breakdown.
Another type of heavy equipment maintenance is specialized maintenance, which involves any task specific to a certain piece of equipment. We'll give some examples below, but it's important to remember that preventative maintenance is important for all types of machinery.

Why Preventative Heavy Equipment Maintenance Matters
Unlike corrective maintenance, preventative heavy equipment maintenance takes a proactive approach to keeping your fleet operational. Corrective maintenance is reactive, and while it's great for getting your machinery back onsite fast, preventative heavy equipment maintenance keeps some issues from arising at all.
By thoroughly inspecting each component for common failure points, heavy equipment maintenance prevents any small issues in your machinery from compounding into larger ones. This makes your fleet more productive in the long run, and reduces your overall downtime — and increases your profitability.
5 Advantages of Preventative Heavy Equipment Maintenance
Preventative heavy equipment maintenance enhances your fleet's overall performance and keeps your team running at its best. The main advantages are:
- Longer Machine Life: Preventative heavy equipment maintenance can extend the life of your fleet by 20-30%. Proactive upkeep means you won't have to purchase costly equipment for years down the road.
- Lower Repair Costs: Which would you rather deal with, a leaky hose or gasket or an entire engine that's seized up from a fluid leak? Preventative maintenance catches component failures early, before they turn into bigger (and more expensive) issues.
- Less Downtime: It may seem like preventative maintenance takes your heavy equipment off the road longer, but in the long run it reduces your downtime. Fixing minor problems is faster than performing major repairs, so preventative heavy equipment maintenance keeps your fleet operational.
- Higher Productivity: Less downtime means higher productivity for your fleet. Teams with a strong preventative heavy equipment maintenance strategy have the tools to complete more projects faster, increasing their productivity.
- Faster Completions: Broken equipment can delay a project, costing your team thousands of dollars or more. Preventative heavy equipment maintenance keeps your vehicles fully operational so that you can complete your projects faster.
Heavy Equipment Maintenance Inspection Checklist
There are several types of heavy equipment maintenance, and each type focuses on a specific aspect of the equipment and should be part of your maintenance program. A few heavy equipment maintenance subtypes are:
- Engine maintenance
- Standard maintenance
- Daily preventative maintenance
Heavy equipment maintenance is essential for maintaining compliance with the leading industry standards. According to the 1926.431 standard by OSHA (Occupational Safety and Health Administration), employers in industries that use heavy equipment must regularly maintain the machines, especially in hazardous locations. Non-compliance with these regulations can result in fines per Section 17 of the OSHA Act. This checklist should help keep you on track.
Engine Maintenance Checklist
Engine maintenance means inspecting and maintaining all the components that keep the engine running smoothly, such as filters, belts, and fluids.
- Check the levels of engine fluids (oil, coolant) regularly.
- Inspect the battery and clean the terminals.
- Check the air filters and replace them when necessary.
- Inspect and clean the cooling system, including hoses, radiators, and water pumps.
- Inspect all hoses for leaks.
Standard Vehicle Maintenance Checklist
A standard vehicle maintenance routine involves inspecting all the major systems, including the engine, transmission, hydraulics, and electrical systems.
- Inspect the hydraulic system for leaks.
- Check the transmission fluid level.
- Inspect the electrical system (battery and starter).
- Check for the dashboard warning lights and address them promptly.
- Test the wipers.
- Check the wheel alignments.
- Inspect the tires for wear and tear.
Daily Preventative Maintenance Checklist
As the name suggests, daily preventative maintenance means performing basic routine checks and maintenance tasks every day before starting the equipment. The operator can do it without much technical knowledge.
- Inspect the exterior of the equipment for any visible damage or leaks.
- Check all the lights (headlights, turn signals, brake lights).
- Inspect and clean mirrors and windows.
- Check the horn and warning signals.
- Check the seat belt for any damages.
- Inspect and clean the cabin area.
- Lubricate all moving parts (hinges, joints) as necessary.
Specialty Equipment Maintenance Checklists
While some maintenance tasks are common to all types of equipment, others may be specific to certain machines. For instance, an excavator may require different maintenance steps than a bulldozer. Here are the heavy equipment maintenance checklists for a few specialized types of machines.
Concrete Pump Truck Maintenance Checklist
A concrete pump transfers liquid concrete from a mixer truck to a designated location, such as a building site.
It is prone to particle contamination since contaminants like gravel and sand can get inside the machine's pipes and pumps. Here are some maintenance tasks specific to concrete pumps:
- Check the hydraulic oil. Replace or clean it if it has a high particulate concentration.
- Replace the hydraulic hose if it is damaged.
- Inspect the electrical elements, such as loose junction boxes, terminal connections, or loose plugs.
- Check for corrosion on the steel pipes.
- Inspect the rubber seals; replace if damaged.
- Replace bad or faulty gaskets on the boom.
- Fix leaky hydraulic fittings.
- Fix or replace malfunctioning electrical components.
Hydrovac Truck Maintenance Checklist
The hydrovac is a combination of a water nozzle and a vacuum. It uses high-pressure water to excavate soil and rocks. The following are some maintenance tasks specific to hydrovac trucks:
- Check the blower's oil levels and change the oil every 250 hours of use or according to the manufacturer's guidelines.
- Grease the drive shaft regularly.
- Replace the filter bags every 1,500 to 2,000 hours of operation.
- Run restriction tests on the machine and replace the filter bags if the restriction levels are high.
- Check the exhaust system for any damage.
- Inspect the vacuum hose regularly for wear and tear.
- Inspect the batteries and charge them if needed.
- Test the hydraulic hoses and replace them if they're compromised.
- Drain the water system, especially in winter, to prevent freezing.
- Check the water pump for signs of damage before winter.
4 Easy Steps for Heavy Equipment Maintenance
Heavy equipment maintenance doesn't have to be hard. Sometimes all it takes is a few easy steps to keep your fleet running like new — and taking the following actions is a good place to start.
1. Identify Major Causes of BreakdownThe best place to start when forming your heavy equipment maintenance protocol is to understand the risks of failure associated with each machine. The three main types of failure are:
- Sudden failure, when a machine suddenly breaks. The cause is usually obvious and can be fixed by simply replacing the damaged component, which is usually damaged due to thermal or mechanical wear.
-
Intermittent failure, when a machine malfunctions spontaneously. It's often harder to identify the cause of this failure mode, as it may be the result of electronic or software failure.
-
Gradual failure, when machine components steadily deteriorate. These parts are usually near the end of their life, and should be replaced before further failure occurs.
Understanding the most common causes of failure can help you form a heavy equipment maintenance strategy so that your team can tackle the highest risks of a breakdown.
2. Properly Train You EmployeesEducation doesn't just promote project safety — it keeps your equipment running well too. Properly training your employees on their equipment helps them run it according to manufacturer specifications, and helps them identify when problems may be arising.
Training also helps alert your employees to potential equipment issues. Once they've been around your equipment long enough, workers may start to notice when something sounds or feels "off." Heavy equipment maintenance training helps them hone in on potential failures so that they can report and resolve them faster.
3. Adhere to Manuals and Guidelines
Construction vehicles come with a long list of resources for proper use. These are created by the manufacturer's designers and engineers, so following them can keep your machinery running at its best. Some of these resources include recommendations for heavy equipment maintenance, such as:
-
When to check certain components
-
Proper fluid levels
-
Best cleaning practices
-
Meaning of signal lights
-
Parts lubrication
Technical manuals also include valuable insights on the best troubleshooting methods for your vehicle, so consult them if any unexpected problems arise in your heavy equipment maintenance.
4. Document Your Service History
Thoroughly documenting your heavy equipment maintenance will help ensure that all vehicles have been inspected in a timely and thorough manner, so be sure to keep a record of your service history. Keeping a thorough record of your service history can also help you support any warranty claims you may submit, helping you save on some costly repairs.
When you document your heavy equipment maintenance history, be sure to include:
-
The date
-
The employee's name who did the maintenance
-
What type of service was performed
-
Any components that were replaced
-
Any components that may need replacing soon
-
The next date of maintenance
-
Any other noticeable issues
You can use an office whiteboard, a booklet kept in your facility or vehicle, or a spreadsheet on a device, but these can prove scattered and inefficient, which weighs down your operations. Fleet management software like RapidWorks' Rapid Fleet offers a centralized, intelligent hub from which you can direct your heavy equipment maintenance workflows. Track repairs and maintenance requests, manage work orders, and generate the reports to demonstrate your compliance — and all from one easy-to-use interface that takes no time at all to learn.
Pro-Tip: Leverage fleet management software like Rapid Fleet to coordinate your maintenance processes, and keep your fleet out in the field for longer.
Preventative Maintenance Tracking
Even with a heavy equipment maintenance checklist, it can be hard to stay on top of all the maintenance tasks for your machinery. If you're managing a large fleet of heavy equipment vehicles, it becomes even tougher. That's where fleet management software like Rapid Fleet comes in.
RapidWorks' preventative maintenance solution, Rapid Fleet automatically tracks equipment usage and mileage while your team works, helping you schedule upcoming maintenance and alerting you when each truck is due. Our tool features a host of preventative maintenance functionalities, including a fleet health overview to see which vehicles need maintenance, and an inspection task queue to ensure that all issues are documented and resolved before your fleet is sent back into the field. The result is a streamlined preventative maintenance workflow that keeps your fleet operational and profitable. Schedule a demo to see how Rapid Fleet can reduce downtime and save you money today.
FAQs
- How can heavy equipment maintenance benefit my operations?
Heavy Equipment maintenance benefits your operations by:
− Extending machine life
− Reducing repair costs
− Minimizing downtime
− Improving productivity
− Reducing project delays - What types of heavy equipment maintenance are there?
The main types of heavy equipment are:
Corrective maintenance, which gets vehicles up and running when issues arise
Preventative maintenance, which keeps your equipment running in top condition
Specialized maintenance, which requires unique tasks for application-specific machinery - What steps can I take to build a heavy equipment maintenance strategy?
A few easy steps in building a heavy equipment maintenance framework are:
− Identifying major causes of breakdown
− Thoroughly training your employees
− Adhering to manuals and guidelines
− Documenting your service history - How can I keep track of my heavy equipment maintenance?
While whiteboards, booklets, and spreadsheets can help you manage your heavy equipment maintenance, the best way to keep track of it is by using fleet management software. These solutions can help you automatically track your equipment usage, schedule upcoming maintenance, alert you when each vehicle is due, and improve your maintenance efficiency.
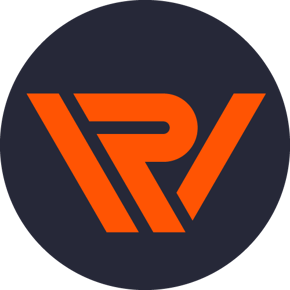